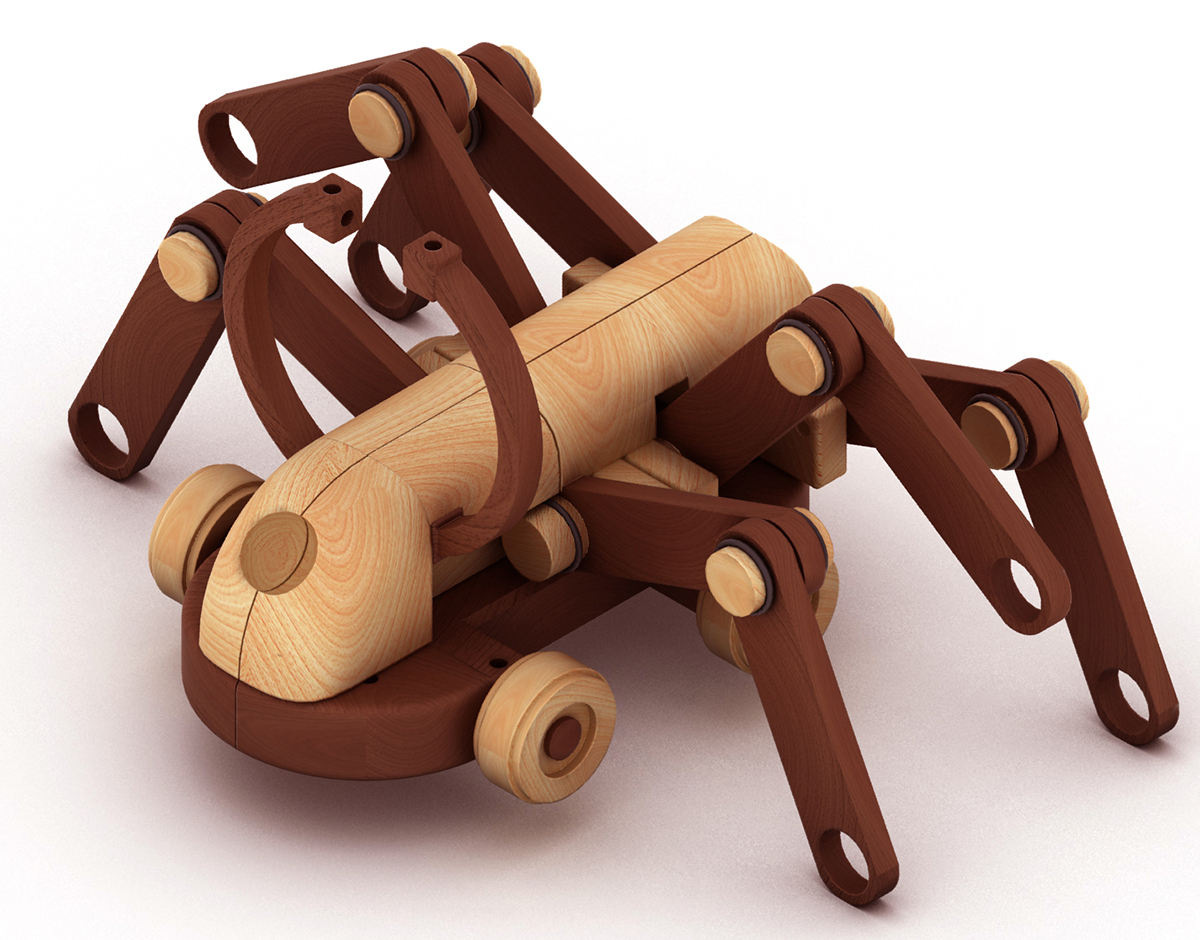
Wooden Toy Designs That Will Delight Parents and Kids Alike
In a world dominated by plastic and screens, wooden toys stand out as a beacon of natural beauty and timeless appeal. Their tactile textures, classic designs, and enduring quality offer a refreshing alternative to the fleeting fads of modern playthings. But beyond their aesthetics, wooden toys possess a unique magic that sparks imagination, fosters creativity, and cultivates a deep connection between children and the natural world. If you're looking for toys that will inspire your child's growth and bring joy to your family for generations to come, look no further than the enchanting world of wooden toy designs.
The Timeless Appeal of Wooden Toys
Wooden toys hold a special place in our hearts, evoking memories of childhood and the simple pleasures of creative play. Their classic designs have stood the test of time, transcending trends and technological advancements. From building blocks to rocking horses, these toys have a universal appeal that resonates with children of all ages and backgrounds.
Durable and Safe
Unlike their plastic counterparts, wooden toys are built to last. They can withstand the rigors of imaginative play and are often passed down through generations, becoming treasured family heirlooms. Their natural materials are free from harmful chemicals and toxins, ensuring a safe and healthy play environment for your little ones.
Fostering Imagination and Creativity
Wooden toys encourage open-ended play, allowing children to use their imaginations to create their own stories and worlds. Unlike toys with specific functions, wooden toys provide a blank canvas for creativity, prompting children to think outside the box and develop their problem-solving skills.
Sensory Exploration and Tactile Learning
The smooth surfaces and intricate details of wooden toys offer a unique sensory experience. Children can explore textures, shapes, and colors, developing their fine motor skills and spatial awareness. The natural warmth and weight of wood provide a comforting and grounding presence, enhancing the play experience.
Inspiring Wooden Toy Designs
The world of wooden toys is brimming with innovative and imaginative designs that cater to diverse interests and developmental stages. From traditional building blocks to intricate dollhouses, here are a few inspiring examples that capture the essence of playful creativity:
Stacking Blocks and Building Sets
Classic stacking blocks offer endless possibilities for building, creating, and problem-solving. Choose from simple geometric shapes or more intricate designs, such as animal figures or alphabet blocks. Stacking blocks help develop fine motor skills, hand-eye coordination, and spatial reasoning.
Wooden Puzzles
Puzzles are a fun and engaging way for children to develop problem-solving skills, spatial reasoning, and fine motor skills. Choose from simple jigsaw puzzles for toddlers to more challenging designs for older children. Wooden puzzles are also a great way to introduce concepts like shapes, colors, and animals.
Wooden Dolls and Playsets
Wooden dolls and playsets inspire imaginative role-playing and storytelling. Choose from traditional dolls, miniature furniture sets, or elaborate dollhouses. These toys encourage children to develop their social skills, empathy, and creativity.
Wooden Trains and Vehicles
Wooden trains and vehicles offer a fun and educational way to explore the world of transportation. Children can create their own tracks, build cities, and embark on imaginary adventures. These toys help develop hand-eye coordination, problem-solving skills, and spatial reasoning.
Wooden Musical Instruments
Introduce your child to the joy of music with wooden musical instruments. From xylophones and drums to ukuleles and guitars, these toys offer a fun and engaging way to explore sound and rhythm. Music is a powerful tool for developing cognitive skills, language skills, and emotional intelligence.
Choosing the Right Wooden Toys
When selecting wooden toys for your child, consider their age, interests, and developmental stage. Look for toys that are well-crafted, durable, and safe. Opt for natural finishes and avoid toys with excessive paint or varnish.
Remember, the best wooden toys are those that inspire imagination, creativity, and a love of learning. With their timeless appeal, enduring quality, and natural beauty, wooden toys are a gift that keeps on giving, fostering a lifetime of cherished memories and playful discovery.